The other side of Apple's shiny surface
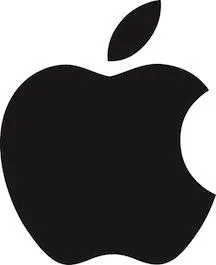
In a follow-up to their detailed story on Apple, "How the U.S. Lost Out on iPhone Work," New York Times reporters, Charles Duhigg and Keith Bradsher attacked the company's alarming safety record at its suppliers in China. In "Human Costs Are Built Into an iPad," the writers reveal that Chinese factory workers producing Apple products often face overwork, injury and death.
"Employees work excessive overtime, in some cases seven days a week, and live in crowded dorms. Some say they stand so long that their legs swell until they can hardly walk. Under-age workers have helped build Apple's products, and the company's suppliers have improperly disposed of hazardous waste and falsified records, according to company reports and advocacy groups that, within China, are often considered reliable, independent monitors."
Apple has responded to the constant stream of unfavorable reports, but slowly and sometimes grudgingly. The company has released an annual supplier responsibility reports, which is "in many cases, are the first to report abuses." But it didn't even identify its suppliers until it released a list in January, 2012, years after investigators have tried to document abuses.
The reporters have focused on Apple's largest supplier, the Taiwanese-owned Foxconn, which, with 1.2 million workers manufactures 40 percent of the world's consumer electronics. In 2006, "... a British newspaper, The Mail on Sunday, secretly visited a Foxconn factory in Shenzhen, China, where iPods were manufactured, and reported on workers' long hours, push-ups meted out as punishment and crowded dorms." Yet, the abuses long continued, to break into view again when, in 2010, 18 Foxconn workers attempted suicide, and 14 of them succeeded.
Apple maintains that it has done what it could, and in fact, "Apple also has trained over a million workers about their rights and methods for injury and disease prevention." But good intentions run aground on the company's harsh policies toward its suppliers, policies no better than the more-reviled Wal-Mart.
"Apple typically asks suppliers to specify how much every part costs, how many workers are needed and the size of their salaries," leaving suppliers "only the slimmest of profits." Consequently, "...suppliers often try to cut corners, replace expensive chemicals with less costly alternatives, or push their employees to work faster and longer, according to people at those companies."
As a result, said a former Apple employee, "You can set all the rules you want, but they're meaningless if you don't give suppliers enough profit to treat workers well... If you squeeze margins, you're forcing them to cut safety."
Another Apple insider despaired of changing the system:
"We've known about labor abuses in some factories for four years, and they're still going on," said one former Apple executive who, like others, spoke on the condition of anonymity because of confidentiality agreements. "Why? Because the system works for us. Suppliers would change everything tomorrow if Apple told them they didn't have another choice."
"If half of iPhones were malfunctioning, do you think Apple would let it go on for four years?" the executive asked.
Neither Apple nor Foxconn are, of course, not the only labor violators operating in China. But Apple is the now the biggest, most profitable consumer electronics manufacturer in the world, with a last-quarter profit of $13.1 billion, and its ugly underside contrasts with its brilliant surface.
Speed Matters believes that every company owes its workers decent conditions and living wages, and Apple is no exception. Many people inside Apple know this, but either can't or won't act on it, and things in China don't appear to be changing for the better. As a former Apple executive said: "We're trying really hard to make things better. But most people would still be really disturbed if they saw where their iPhone comes from."
Well, now we know, and maybe it's up to Apple's millions of devoted customers to pressure the company's leaders to sacrifice a few of their profits and stock options to ensure that the people who make their products - wherever they are - are safe and fairly paid.
How the U.S. Lost Out on iPhone Work (Charles Duhigg and Keith Bradsher, The New York Times, Jan. 21, 2012)
Human Costs Are Built Into an iPad (Charles Duhigg and Keith Bradsher, The New York Times, Jan. 26, 2012)
Apple Supplier Responsibility website
Broadband Brigade members turn out to protect good, union jobs and reliable broadband service
CWA condemns Trump NTIA changes to BEAD funding policies